A simple test confirmed what most people already estimated for an “efficient” cast aluminum frame of the Cybertruck. It’s very weak and only gets weaker with each use.
“The Cybertruck is not a rigid stainless steel exoskeleton supertruck, like it was advertised. It is a soft, supple, porous, Mohs 3 level cast aluminum (truck) with the towing ability of a pop can.” The Cybertruck’s rear subframe [advertised as 11,000 pounds capacity] totally shattered with about 10,000 pounds of force on the hitch. […] “A cast aluminum frame with just 3/16ths wall thickness is just a slap in the face to anyone who bought one of these Cybertrucks,” says Nelson.
Pop can. Shattered. Slap in the face.
Not what a truck “rated” for towing is supposed to mean, certainly not. You’d be safer towing with a Toyota Prius.
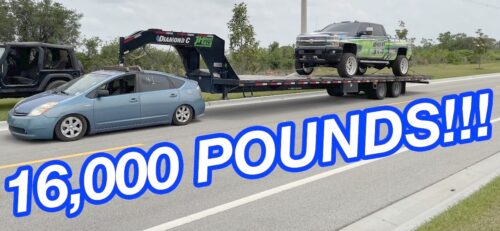
You’ve all stumbled onto the sage wisdom of the ages that aluminum is a terrible frame material for stress. This NIST paper confirms what you are saying here, published in 1950
https://nvlpubs.nist.gov/nistpubs/jres/045/6/V45.N06.A03.pdf
I believe public discussion of product safety based on scientific evidence is essential for consumer protection and product improvement. You are providing valuable context and motivation for understanding materials science principles. If anyone disagrees with these independent testing results, they should respond with their own data and testing about potential safety concerns. The fact that the tongue stress failure appears unsafe at basic load, with no wiggle room, suggests this design was never properly vetted.
@Robert
Thank you for sharing this research paper. It’s interesting to see scientific documentation from NIST on aluminum’s fatigue properties dating back to 1950. The paper highlights some fundamental engineering concerns about cast aluminum, particularly how it can weaken under repeated stress cycles.
While this research predates modern manufacturing techniques and alloy development, it does explain the basic principles of why cast aluminum is so problematic in high-stress applications. Tesla’s decision to use cast aluminum for a component subjected to significant towing forces needs greater scrutiny, especially given what materials science has long warned about its weaknesses.
The paper’s findings about aluminum being “more prone to cracks and failures” without additional mechanical processing seems particularly relevant to what the JerryRigEverything test demonstrated. I appreciate you bringing in this technical perspective to the discussion.
Interesting blog and especially interesting blog post. I am happy to have discovered this today. I’ve been teaching materials science and mechanical engineering for decades. Now I have to use the Cybertruck’s implementation of a cast aluminum frame for towing applications as an example of failing fundamental physics.
This experimental product gets an obvious F due to a clear failure by design. It never should have been put into production.
Any student of mine is not going to attach a steel receiving hitch directly to a cast aluminum frame, given basic materials science principles. BASIC science. Cast aluminum is a temporal weight savings material, meaning intrinsically different mechanical properties that make it completely unsuitable for high-stress cyclic loading work applications like being a truck, let alone for towing.
The cast aluminum fatigue behavior follows an S-N curve with no horizontal asymptote, meaning that ALL cyclic stress levels, even the lowest ones, eventually lead to FAILURE. Let me say it again, the Cybertruck IS A DESIGN OF CATASTROPHIC FAILURE. Unlike steel, aluminum is well known to possess NO ENDURANCE limit.
Class, I want you to STOP. Look around you. Look at every person, look in their eyes, understand your duty of care. Gross negligence means knowingly causing harm or creating substantial risk of harm, a reckless disregard for safety. This design violates baselines of safety, and anyone in the chain of production with a basic grasp of physics would have been justified to pull an alarm to stop it. We face civil liability through courts, we face state-level regulatory actions, we face public scrutiny and consumer advocacy.
The porosity inherent to a the aluminum casting process of this vehicle frame means it has predictably consistent microscopic stress concentrations, which essentially mean crack initiation spots WHEN subjected to tensile loading. NOT IF. Throughout the material, known to any engineer qualified to be working on it, stresses are calculated as sigma_local = K_t × sigma_nominal, where K_t (the stress concentration factor) and go significantly higher at casting defects. The case for gross negligence is easy to see.
Given all that, the interface from aluminum to steel then creates additional complications due to galvanic coupling and differential thermal expansion (alpha_aluminum = 23 × 10^-6/°C vs alpha_steel = 12 × 10^-6/°C), which induces interfacial stresses during temperature fluctuations.
NOW YOU SEE, students, that anyone advertising the 11,000-pound towing capacity from a structural system that catastrophically fails at 10,000 pounds of vertical loading represents a CATASTROPHIC SAFETY HAZARD TO THE PUBLIC BY DESIGN. When we consider that dynamic loading from road irregularities can easily multiply static forces by factors of 1.5-3x, the safety margin becomes dangerously negative.
What’s particularly egregious is that these failures aren’t even going to be any kind of random or rare “black swan” event, because they’re the EXPECTED and PREDICTABLE OUTCOME of first-principles materials physics.
Any competent stress analysis reveals these vulnerabilities, which is what you’re watching in the video. The fact that the safety hooks also failed indicates a FUNDAMENTAL FLAW in the entire load path design. These Tesla engineers are magnitudes worse than anything we saw in the VW diesel scandal. Management should be facing courts.
In my classroom, we have now a tragic example of why material selection must be driven by application-specific requirements rather than efficiency, drugs, fantasy fiction, profit, manufacturing convenience, weight reduction goals, or whatever else led to this negligence.
A cast aluminum frame has been known for decades to be unsuitable for almost all general vehicle architecture, and dismissed as a luxury high-cost disposable concept (e.g. race car with a 24 month lifecycle). To be clear, I could assign some specialized cast aluminum alloy projects for students to report on automotive usage of fatigue properties improved above the best casting methods, but they fundamentally can not escape the lack of true endurance limits and will NEVER, ever pass the class if they attempt high-load applications like towing
Attaching high-load towing components to a cast frame without logical fail-safe reinforcement engineering demonstrates the kind of “efficiency” mindset of a cheat, a fraud, a scam that kills. The laws of physics are LAWS. Marketing claims held above the basic engineering fundamentals are a clear and present threat to public safety. Don’t wave a loaded grenade launcher in a crowded theater.
This isn’t just an F project in science and engineering. This is a trip to the school psychologist for therapy evaluation.